Introducing the SideRider
- Spencer Maynes
- Feb 26, 2024
- 3 min read
Updated: Mar 4, 2024
Deflect LLC is proud to announce the SideRider, a new innovation to improve the aerodynamics of Autoracks. Long-lasting and easy to install, the SideRider can help rail companies lower fuel consumption, reduce greenhouse gas emissions, and increase their competitive edge against the trucking industry.

Autoracks are a keystone of North America’s rail and automotive industries: transporting passenger cars, trucks, and SUVs in the most fuel and cost efficient way from manufacturers to customers. Thanks to lower aerodynamic drag and wheel resistance, they can transport cars at only one half the emissions per ton mile compared to trucks according to the Federal Railroad Administration in a 2009 study. Though these savings are considerable, the table below shows that they are likely lower than those obtained from other commodity types, illustrating how much room there is to improve the efficiency of Autoracks. The booming economy in the US makes this even more critically important, with vehicle sales up 13% in 2023 and rail miles for automobiles up 12%.

Considerable improvements have already been made to the aerodynamics of Autoracks since 2009. Many current vehicles including the Greenbrier Multi-Max have features such as interior ladders, which can reduce aerodynamic drag and fuel consumption while also improving safety. Our own Computational Fluid Dynamics (CFD) simulations show that moving these ladders inside decreases aerodynamic drag by an estimated 12.5% on Automotive trains, meaning a likely ~4% decrease in fuel consumption. The visualization below from our simulations shows the bright red area of pressure drag that occurs in front of external ladders and how moving them to the inside can improve flow. However an unfortunate side effect of removing the ladders is that pressure on the front face of the following car increases as airflow into the inter-car gap is no longer blocked. This can be seen from the orange area in the graphic.
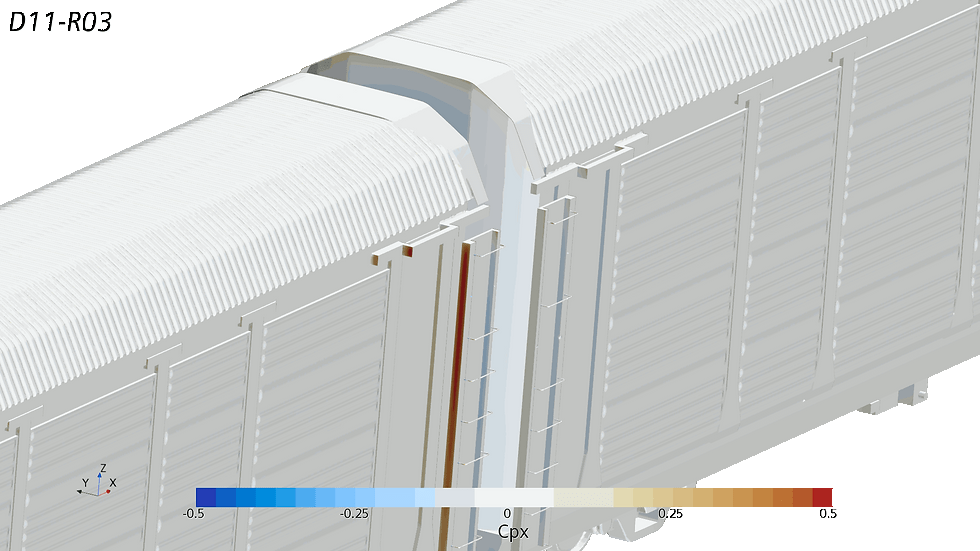
Our own patented product, the SideRider for Autoracks, can be utilized to cure this pressure drag in the inter-car gap. Placed on the side of railcars, it gently deflects air around the gap and past the front face of the following car. It can be seen in orange in the image below. The SideRider will work with the Autorack traveling in either direction, lasting for the life of the railcar with no foreseen maintenance or operational work needed at any time and at minimal cost for the railcar owner.

We have tested a variety of SideRider designs in CFD and their impacts can be seen in the next image. As the deflector increments in height from nonexistent all the way to 1.5 inches, the red area on the front face of the following railcar where airflow impinges and strikes goes down in size and there is also a smaller offsetting increase in drag at the location of the deflector, the balance between these determines the optimal size of the SideRider. Our current best performing option in simulations shows an 8.1% decrease in drag on the second full Autorack where it is equipped. On a 100 car train with unequipped locomotives at the front, this corresponds to a total benefit of ~7%. As a rule of thumb, fuel savings usually correspond to about 30% of drag savings on freight trains, indicating that the SideRider could lower fuel consumption on equipped trains by over 2%. As some US class 1 railroads spend billions of dollars on fuel annually, this is a significant cost savings measure.

We will be testing further SideRider designs in CFD and on a scale model in the wind tunnel over this summer to optimize our design and prove it at various yaw angles and conditions. By the end of 2024, we believe that the SideRider’s effectiveness will be proven and that it will be reducing resistance for the world’s most efficient way of transporting cars over land. The freight rail industry is critical for lowering carbon and particulate pollution worldwide. Our products the RoofRider and SideRider can help twice over by directly reducing rail emissions and helping rail competitively against trucking.
Comments